Магия технологий, или О том, как разрушить шаблон-тормоз
На новые рельсы
Сегодня в этом масштабном процессе задействовано 60 предприятий региона. На каждом из них внедрили технологии бережливого производства. А помогли компаниям встать на новые рельсы специалисты Регионального центра компетенций (РЦК) – структурного подразделения Фонда развития промышленности Пензенской области.– Мы выезжаем на предприятие, участвующее в нацпроекте, и на месте выясняем, что мешает сотрудникам выполнять свою работу, – рассказывает руководитель РЦК Павел Ивчатов. – А это потери, то есть операции, на которые затрачиваются ресурсы, но товар для потребителя не становится более ценным: например не улучшается качество, не увеличивается скорость изготовления. Основа бережливого производства – сокращение потерь, их необходимо своевременно выявлять и оперативно устранять.
Специалисты РЦК проходят на производственной площадке весь путь изготовления товара (от склада сырья и материалов до отгрузки готовой продукции), изучая все вместе с сотрудниками компании.
Проанализировав выявленные проблемы, предлагают решения по оптимизации и стандартизации процессов производства, грамотному обустройству рабочего пространства, совершенствованию управления, логистики и сбыта.
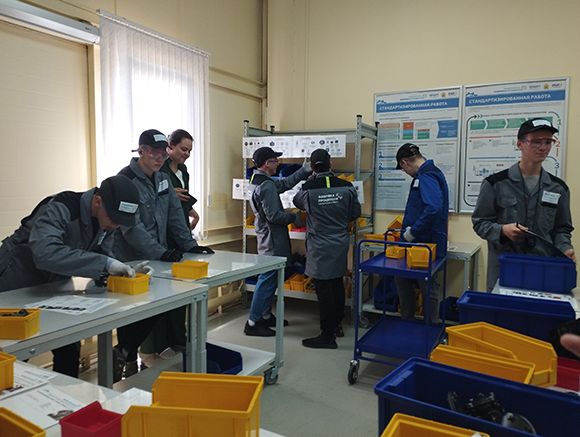
Не просто игра
Для того чтобы коллективам было проще перейти на новую систему работы, при РЦК создана «Фабрика процессов» – учебно-производственная площадка, где на практике осваиваются инструменты бережливого производства. Обучение здесь построено как бизнес-игра: команда под руководством тренера за определенное время должна собрать из 40 деталей пульт управления регулятора давления газа – реальное изделие, применяемое в газовой отрасли. Причем необходимо стремиться к результату – 10 готовых изделий за 20 минут.Атмосфера в бизнес-игре всегда оживленная.
– Давай, разбирай скорее, у нас всего 20 секунд осталось!
– Помоги, а то не успеем!
Это торопятся и шумят, боясь не выполнить задание, студенты Пензенского колледжа архитектуры и строительства – на «Фабрике процессов» учатся не только работники предприятий.
– Неважно, чем в повседневной жизни занимаются наши участники: металлообработкой или сбором огурцов в промышленных масштабах, – принципы бережливого производства одинаковы для всех, – поясняет тренер РЦК Евгений Синяев. – Ведь главная цель обучения – не собрать деталь, а научиться выявлять и устранять проблему, снижающую производительность труда.
Оказывается, тормозить процесс могут даже неправильно подобранные рабочие перчатки, с чем столкнулись во время обучения студенты.
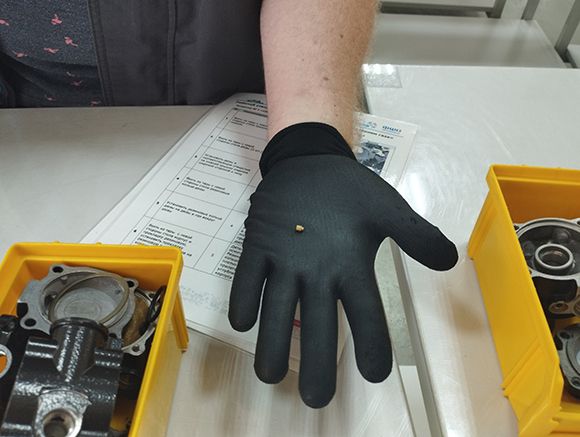
Выданные им на складе стандартные хлопчатобумажные с ПВХ-покрытием «точка», подходящие для садово-огородных дел, оказались неудобными при сборке мелких деталей. После замены на прорезиненные и более плотно прилегающие к пальцам операция пошла в разы быстрее.
– Или такая ситуация: стеллажи с готовым изделием стоят в одном конце цеха, а склад – в противоположной стороне. чтобы отвезти туда продукцию, приходится преодолевать расстояние в несколько десятков, а то и в сотню метров, – делится впечатлениями первокурсник Алексей Малышев. – Из-за того, что стеллажи не разгружаются вовремя, некуда складывать новые собранные детали, соответственно, замедляется работа на всех предыдущих этапах. А всего-навсего надо установить их поближе к складу.
И все-таки удивили
Технический директор АО «ЦеСИС» Лев Просвирнин часто цитирует знаменитого английского писателя-фантаста Артура Кларка: «Любая достаточно развитая технология неотличима от магии».– Мы первыми в Пензенской области вошли в нацпроект «Производительность труда» в 2019 году, и все, что произошло на предприятии за эти пять лет, действительно напоминает магию, – уверяет Лев Владимирович.
Технологию бережливого производства в этой компании, разрабатывающей и выпускающей инновационные комплексы физической защиты для режимных объектов, апробировали в процессе изготовления одной из секций заграждения.
Поначалу идею приняли прохладно. Предприятие и без того числилось в передовых, здесь существовала сложившаяся система ведения бизнеса, были отработаны все технологии.
– Казалось бы, ну что такого нам могут предложить, чего мы не знаем? – рассказывает Лев Просвирнин. – Но поскольку привлечение специалистов центра компетенций и обучение были безвозмездными для компании, мы снисходительно кивнули головами, мол, давайте попробуем.
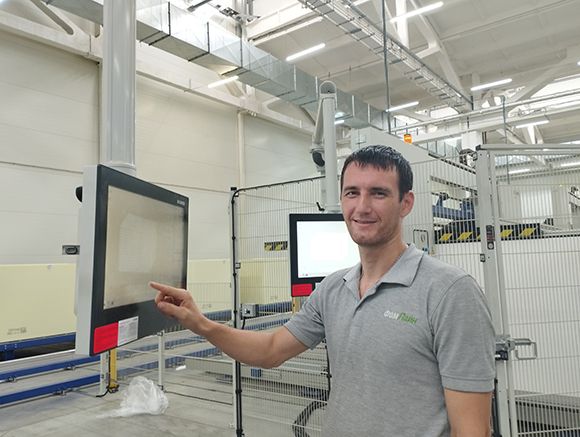
Вскоре выяснилось, что производственных запасов у нас накопилось в 33,5 раза больше, чем необходимо, а ведь на потраченные на них миллионные средства можно было бы, например, купить новое оборудование.
На одной из операций работали четыре человека – оказалось, то же самое вполне могут выполнять двое: достаточно было лишь увеличить размер приемного стола. Высвободившиеся кадры направили на другой участок, где нужна была дополнительная сила.
Много сил и времени уходило на то, чтобы при изготовлении определенных деталей вручную обрезать с боков каждой излишки металла. Обнаружилось, что лишнюю операцию пришлось выполнять из-за сбоя станка, который давно уже вместо положенных 1,5 мм припуска на обработку начал выдавать 10 мм.
И это только часть потерь, которые выявили специалисты и которые не замечали опытные сотрудники предприятия – у них, что называется, глаз замылился.
– Результаты проекта по повышению производительности труда превзошли все ожидания, – констатирует Лев Владимирович. – Представьте, пять лет назад у нас процесс на этом потоке с момента завоза материала и до выхода готовой продукции занимал 54 дня, а теперь – всего четыре! Один рабочий в среднем стал производить в три раза больше продукции, при этом нагрузка не увеличилась – все дело в грамотной организации труда.
Не только технологии
ООО «Кузнецкий технопарк», где производят матрасы и комплектующие к ним, предприятие относительно молодое, – ему нет еще и 10 лет. Компания шагает в ногу со временем, используя новейшее оборудование и современные технологии.Однако и здешнее руководство вместе с коллективом после вступления в нацпроект в конце 2021 года узнало много нового о своем производстве. Специалисты РЦК выявили около 50 проблем, снижающих эффективность работы.
Например, оказалось, что на участке изготовления пенополиуретана процесс застопоривается из-за неправильно расположенных станков. На одном, нарезающем длинномерные блоки застывшей пены на более мелкие, работа вставала, потому что линия оказывалась перегруженной полуфабрикатами. Их просто не успевали вовремя перевезти на второй станок, расслаивающий изделия на тонкие листы, – он находился на расстоянии 25 метров от первого. Отсюда простои и на следующих этапах.
– Пришлось поменять логистику на участке, добавить конвейеры. Мы изменили программное обеспечение на определенном участке, что позволило загружать линию автоматически, без участия человека – раньше процесс регулировал оператор, – поясняет заместитель генерального директора предприятия по производству Семен Манечкин.
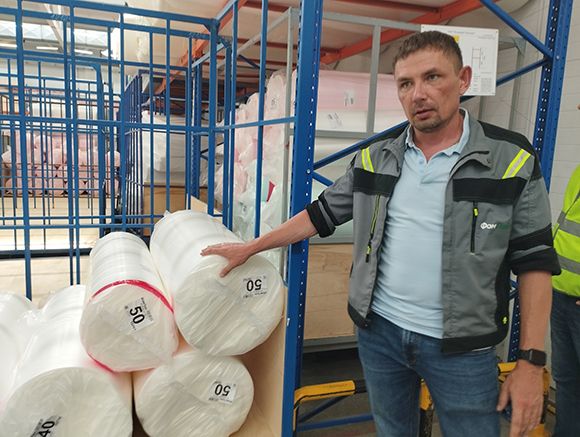
Кстати, рабочие, которые изначально также с недоверием отнеслись к новым веяниям, не только быстро смогли перестроиться, но и внесли рацпредложения.
Резчик Василий Прокин сконструировал платформу, благодаря которой стало значительно легче и удобнее разрезать пенополиуретановые рулоны. Раньше рабочим приходилось делать это с постоянно поднятыми руками, так как конвейер располагался на высоте человеческого роста. Долго ли можно продержаться в таком положении?
– Я проштудировал весь Интернет, пока не нашел решение проблемы, – поделился Василий. – Идею создания платформы, по которой рабочий может подняться на нужную высоту, поддержало начальство, конструкторы разработали макет – на его основе мы и изготовили устройство.
Благодаря всем мерам, на выбранном потоке на 64 процента сократилось время изготовления продукции и на 29 процентов выросла выработка.
Вот таким образом участие в нацпроекте помогает предприятиям увеличивать объемы производства, улучшать условия труда рабочих, повышать их квалификацию и уровень заработной платы (а это самая лучшая мотивация).
Но это при условии, что коллектив является единым организмом, где каждый воспринимает потери на рабочем месте как свои собственные и стремится улучшить ситуацию. Где руководство способно разбить шаблон, к которому все привыкли.
Основные критерии для участия в нацпроекте «Производительность труда»
– Выручка предприятия – от 400 млн рублей за минувший год.
– Предприятие должно относиться к одной из базовых несырьевых отраслей: обрабатывающее производство, сельское хозяйство, транспорт, строительство, торговля, туризм.
– Доля участия иностранного учредителя в уставном капитале не должна превышать 50 процентов.
Цифры
60 предприятий Пензенской области являются участниками нацпроекта «Производительность труда». Из них:
48 – относятся к обрабатывающей промышленности,
6 – к сельскому хозяйству,
3 – к ЖКХ,
1 – к транспортной отрасли,
2 – к строительной.
Историческая справка
Создателем концепции бережливого производства считается японец Тайити Оно, создавший систему в Toyota в 1950-е годы. Однако сегодня только специалисты знают, что в основе лежат идеи советского ученого, теоретика научной организации труда Алексея Гастева.
В 1920 году он основал Центральный институт труда, занимался улучшением организации рабочих мест, оптимизацией процессов, подготавливал кадры и совершенствовал формы разделения труда. Спустя некоторое время научную деятельность Гастева начали активно критиковать. В фаворе было стахановское движение с его трудовыми подвигами, несовместимыми с рациональным планированием.
Закончилось все печально. В 1938 году Алексей Капитонович угодил под каток Большого террора. Ученого арестовали, а в 1939-м расстреляли. Его институт был закрыт в 1940 году.
Автор: Наталья СИЗОВА
Нашли ошибку - выделите текст с ошибкой и нажмите CTRL+ENTER
Другие материалы рубрики
Арина Родионовна от соцзащиты: история пензячки Елены Купцовой
В Пензенской области в рамках нацпроекта «Семья» появились первые социальные няни20 лет за рулем троллейбуса: пензячка Алла Мельникова – о нелюбимом маршруте, автохамах и стычках с водителями автобусов
Рассказываем ее историюПензенские медики рассказали, как сохранить здоровье в школе
Биография Николая Ларюшина: карьера в ПГАУ, отказ от переезда в США и отношение к современной технике
Магия руци и паци: жительница села Старое Славкино хранит культуру своих предков
Вместе больше полувека: история любви супругов Беляниных из Русского Камешкира

Пензенский драмтеатр открыл сезон спектаклем «Яма» (2025)
Музыка и декорации драмы продуманы до мелочей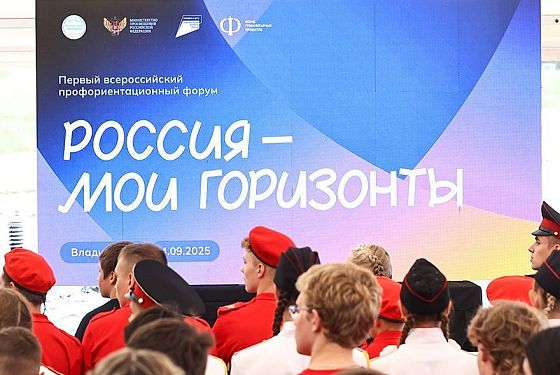
В пензенских школах начался новый сезон курса «Россия – мои горизонты»
4 сентября состоялось первое установочное занятиеСемья Бутусовых переехала из Пензы под Сосновоборск ради фруктов и ягод
Вопреки пословице «Где родился, там и пригодился», они нашли свое дело вдали от дома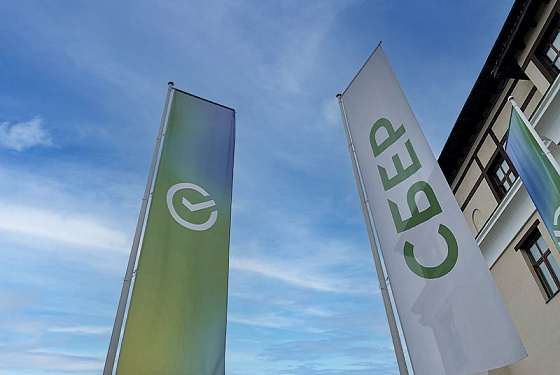
Время создавать будущее: Сбер открывает регистрацию на AI Journey Contest с призовым фондом 6,5 млн рублей
К участию приглашаются AI-профи со всего мира, а награждение состоится на AI Journey 2025Сбер и ВЭБ приступают к работе по созданию единого стандарта и новой модели финансирования ГЧП
Бесконечная кредитная линия: инновационное решение Сбера может стать новым стандартом рынка
Сбер и «Дамате» запустили первое в России товарное РЕПО на фуражную пшеницу
Александр Ведяхин: юбилейная X конференция AI Journey пройдёт в Москве с 19 по 21 ноября