Руководитель ЭМИ Сергей Качкаев: К долгим совещаниям у меня отвращение
Однако за сегодняшними успехами стоит очень много труда, энтузиазма, учебы на собственных ошибках. О своей «дороге в тысячу лье» рассказал руководитель предприятия Сергей Качкаев.
Как начиналось свободное плавание
— Сергей Николаевич, как все начиналось?— Просто захотелось оставить свой след на земле. Свободных ниш в то время было много, в дефиците было буквально все, но решили заняться тем, в чем были профессионалами, – конструированием. Сняли полуподвальное помещение в доме № 2 на ул. Володарского и отправились в свободное плавание.
Поначалу перспективы были заманчивыми. Мы выиграли тендер на разработку и поставку электронных весов для системы «Витязь» (она использовалась для ликвидации последствий чернобыльской аварии) и получили заказ на 3 тысячи изделий. Если бы контракт был выполнен в полном объеме, то через три года наше малое предприятие вышло бы на уровень производства, которого в итоге удалось достигнуть только спустя 15 лет. К сожалению, до развала СССР мы успели продать всего 142 изделия, а потом программу закрыли.
Не хуже рижан
— Сейчас предприятие специализируется на выпуске автомобильных компонентов. Как получилось, что вы заняли именно эту нишу?— Оставшись без работы, мы брались за все: разрабатывали измерительные системы, противоугонные устройства. Потом до нас дошла информация, что на российском рынке есть перебои с автомобильными датчиками, которые в СССР производил один завод — в Риге.
Весной 1992 года в Пензу даже приезжали представители Министерства машиностроения страны, собирали руководителей крупных заводов и предлагали освоить производство автодатчиков. Но наши промышленники посчитали, что это сложно, и отказались.
А мы решили попробовать. Меньше чем за месяц сделали 12 опытных образцов и отправили их на АЗЛК и на Уфимский завод автомобильных моторов. Через две недели от последнего пришла телефонограмма: «Срочно приезжайте заключать договор, ваши датчики прошли испытание». Так мы получили первый заказ на 50 тысяч изделий, которые нужно было сделать за четыре месяца.
А у нас не было ни собственного оборудования, ни денег. Шел 1992 год. В долг никто не давал, в счет будущих поставок — тоже. Пришлось брать кредит под 15 процентов в месяц (не в год!).
Работали в прямом смысле на коленке: настройку первых датчиков проводили с помощью автомобильных насосов, а запрессовывали домкратом. Закатывали их токари с завода «Электромеханика», которые приходили к нам в подвал по вечерам после своей основной работы. Детали по нашим чертежам были изготовлены на пензенских заводах.
В общем, в августе я привез на уфимский завод 118 датчиков. Меня никогда в жизни так радостно не встречали: водили по всем отделам, показывали как диковинку и говорили: «У нас теперь, наконец, есть датчики, их сделали в Пензе!» Мы были первыми в стране, кто освоил производство этих деталей. Первый заказ был выполнен точно в срок.
Простой секрет
— Сегодня завод ЭМИ — одно из наиболее стабильных предприятий региона. В чем залог успеха?— Успех всегда создают люди. У нас замечательный коллектив, нет текучки кадров. Даже в 2008 году, во время тяжелейшего экономического кризиса, никто не уволился.
Наши сотрудники умеют работать и выполнять поставленные задачи. Приведу такой пример. В 2015 году у Брянского автомобильного завода возникли проблемы с одной из запчастей (выключатель света заднего хода). В мае нам пришло с завода письмо с предложением освоить выпуск данной детали.
Раньше мы подобные выключатели не делали. Я пригласил начальника инструментального цеха и разработчиков из КБ, и после недолгого обсуждения было принято решение серийно освоить выпуск данной детали. Через девять дней выключатель лежал у меня на столе. Я тогда испытал настоящую гордость за коллег: с нуля были разработаны собственная конструкция, чертежи пресс-формы, штампов, техоснастка и все изготовлено.
Уверен, что эту задачу за такой срок не выполнил бы ни один завод в России. Увязли бы в совещаниях. На российских заводах еще с советских времен работа поставлена так, что без долгих совещаний и планерок ничего с места не двигается.
— А у вас на предприятии по-другому?
— Именно. К долгим совещаниям у меня отвращение с молодости. В 1985 году после армии я устроился работать на ЗИФ в 124-й цех. Это была великолепная школа, но как неэкономно расходовалось время сотрудников! Утренняя «пятиминутка» у начальника цеха, где собирались все мастера, начиналась в 7.00, а заканчивалась в 11.00. Плюс вечерняя планерка — с 17.00 до 19.00. И так каждый день. При том что наш цех выпускал всего два вида продукции: рама велосипедная — женская и мужская.
Я против того, чтобы отрывать людей от работы. Моя задача как руководителя — обеспечить производство всем необходимым. А начальники цехов должны выполнить программу по выпуску продукции. Чиновничий аппарат у нас минимальный — по сути, это директор и бухгалтерия. Более 80 процентов составляют рабочие, а небольшое КБ ежегодно разрабатывает по 8–12 новых изделий.
Общие совещания проходят у нас один раз в месяц, 7-го числа (так называемый час качества), а по вечерам начальники цехов приносят мне отчеты о том, что было сделано, и через пять минут мы расходимся.
То, что не убивает, делает нас сильнее
— Как на предприятии отразились экономические кризисы?— По полной программе. Сначала была борьба за выживание в 90-е. До сих пор удивляюсь, как мы выжили в тот период. Все деньги, которые появлялись, шли на погашение кредитов, закупку металла. Несколько лет жили фактически за счет своих родителей-пенсионеров. Но график отгрузки не сорвали ни разу.
Но это был колоссальный урок: мы поняли, что надо расширять ассортимент, занимать рынок, загружать людей другой работой. Если в 2007 году мы выпускали 49 деталей, то сегодня – 217.
— Как вы оцениваете современное состояние рынка машиностроения?
— Надо реально смотреть на вещи: доля отечественной продукции, к сожалению, снижается. Поэтому расслабляться нельзя — колебания происходят постоянно. И мы работаем по максимуму, чтобы быть готовыми к любому развитию событий на рынке. Основной акцент — на качество, ведь наши изделия используются на крупнейших автомобильных конвейерах России. А такое доверие дорогого стоит.
Цифры
В настоящее время завод производит более 200 изделий собственной разработки. Поставляет их более чем 800 заказчикам в России (в том числе на 17 крупнейших автомобильных заводов страны), 16 — в Белоруссии и 6 — в Казахстане.
Автор: Елена СВЕРДЛОВА
Нашли ошибку - выделите текст с ошибкой и нажмите CTRL+ENTER
Ссылки по теме
Другие материалы рубрики
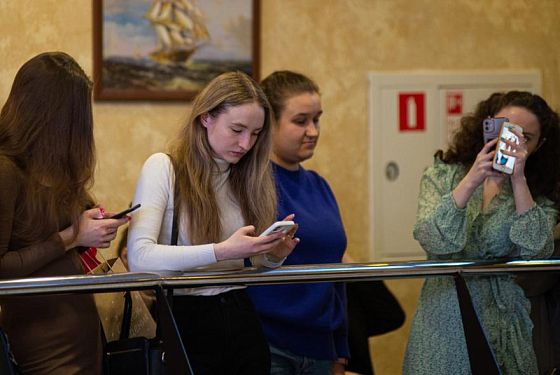
Вне зоны доступа: как справляются пензенцы с перебоями мобильного интернета
В Пензенской области появились очереди к банкоматам. Люди снимают наличные, потому что не всегда могут расплатиться картой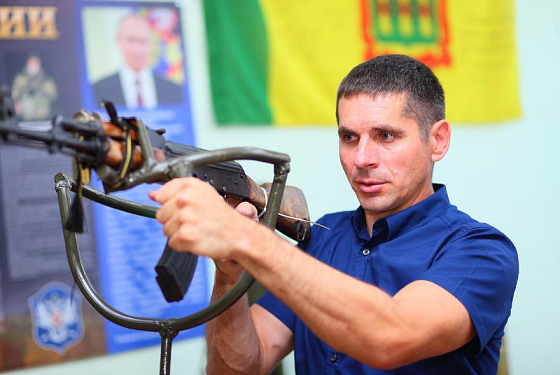
В Пензе бывший кукольник разрабатывает ловушки для дронов
Было время, когда Алексей Большаков увлекался кукольным театром и сочинял сказки. Сегодня он активно помогает фронту«Щукари» не сдаются: как кузнецкий рыбак занялся спасением прудов
Зависимость – не приговор материнству: в Пензе помогают женщинам избавиться от тяги к спиртному
«Нас все бросили»: родители-воспитатели 5 детей выживают в развалюхе под Пензой
Один против расстояния: парень из Колышлея отправился в Таиланд на велосипеде

Куда сходить на День знаний в Пензе 1 сентября 2025: праздничная программа
Публикуем афишу самых ярких событий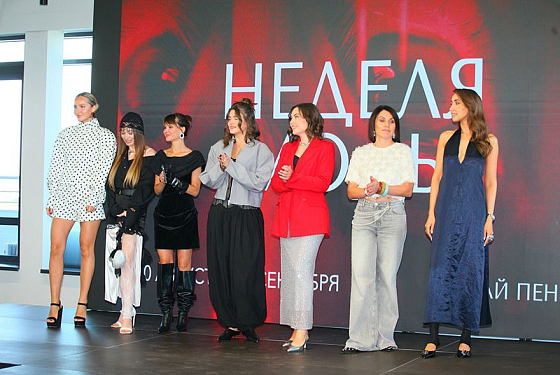
В Пензе победителем «Битвы стилистов» стала Алина Сарабьева
Она сумела поразить жюри преображением своей героиниВ Пензенском драмтеатре впервые ставят спектакль по Куприну
В Сочи пройдет выставка памяти фотокора «Пензенской правды» Владимира Гришина
7 лучших идей, куда сходить на выходных в Пензе 30 и 31 августа 2025: спектакль «Человеческий ресурс» и фестиваль «КлассикУм»
Звезда «Молодежки» Канопка ответил на вопросы пензенцев
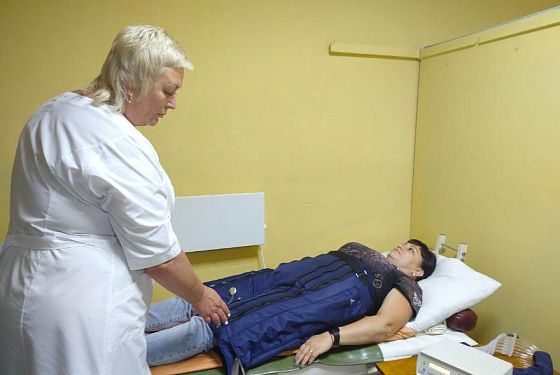
В отделение реабилитации Сердобской больницы закупили новое оборудование
Оборудование приобретено по федеральной программе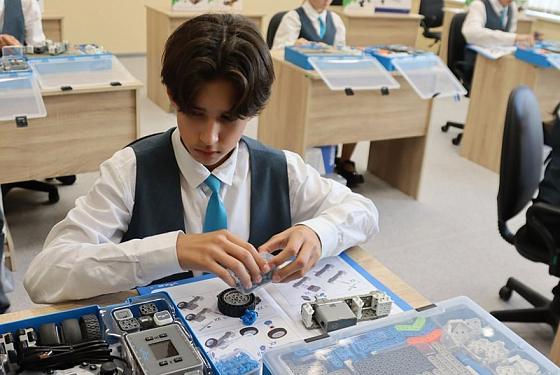
Более 120 тысяч юных пензенцев активно занимаются в различных кружках и секциях
Дополнительное образование дает дополнительные преимущества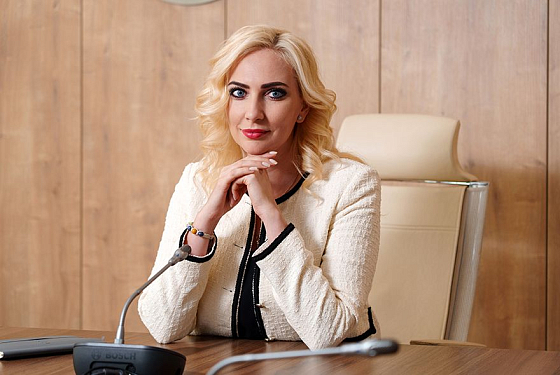
Направление корпоративно-инвестиционного бизнеса в Поволжском банке Сбербанка возглавила Наталья Михайлова
Общий стаж в банке нового топ-менеджера – 20 лет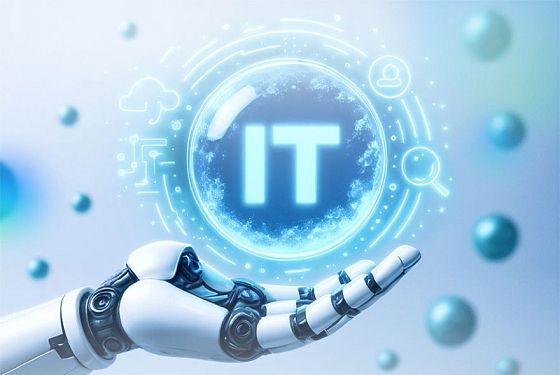
Продолжается регистрация на конкурс по искусственному интеллекту AI Challenge для школьников и студентов
Регистрация продлится до 22 сентября 2025 года
Учёные Сбера предложили новый способ борьбы с галлюцинациями моделей искусственного интеллекта
Стейк хаус в Москве: гастрономия, стиль и современный ритм
Сбер: самые востребованные специальности Поволжья для образовательного кредита — юриспруденция, журналистика и IT
Каждый десятый житель Пензы формирует сбережения на оплату образования
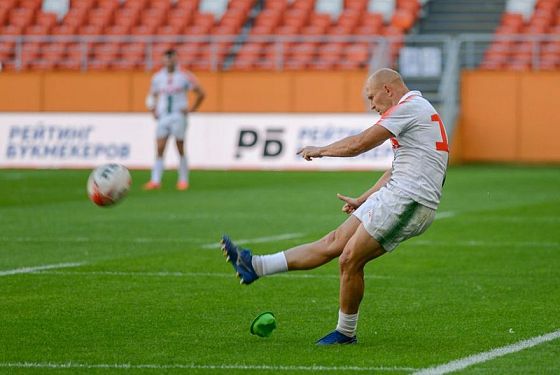
В финале PARI Кубка России по регби сыграют «Локомотив» и «Стрела-Ак Барс»
Это первый финал Кубка России по регби без красноярских команд за 21 год